Production Process
At SUPER POWER, we are committed to maintaining the highest standards of quality throughout our production process. Our rigorous quality control protocols and state-of-the-art manufacturing techniques underscore our dedication to delivering generator sets known for their reliability and performance. With an unwavering pursuit of excellence, we continually refine our processes, ensuring that every product bearing the SUPER POWER name reflects our steadfast commitment to quality.
If you need more details about our factory, please don’t hesitate to contact our team immediately, we will give you the most professional reply in the fastest time within 12 hours!
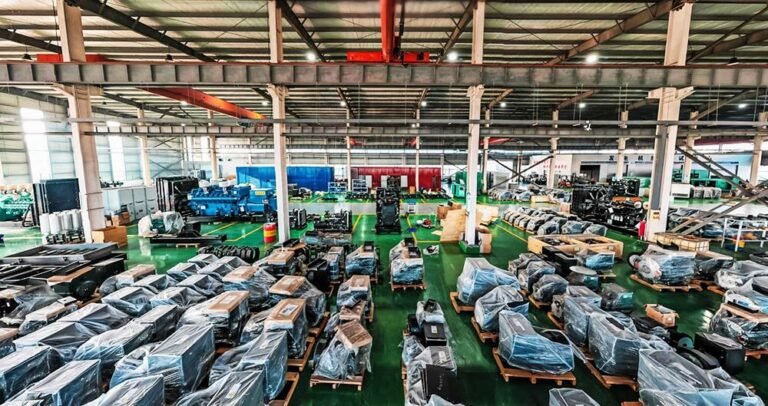
workshop(Incoming inspection area)
Acceptance of incoming materials, before the installation of diesel generator sets will be strictly in accordance with the design drawings, order requirements to check every material.

Laser machine
Cutting of steel plates according to drawings, precise cutting according to the shape and size of the customized silent canopy.
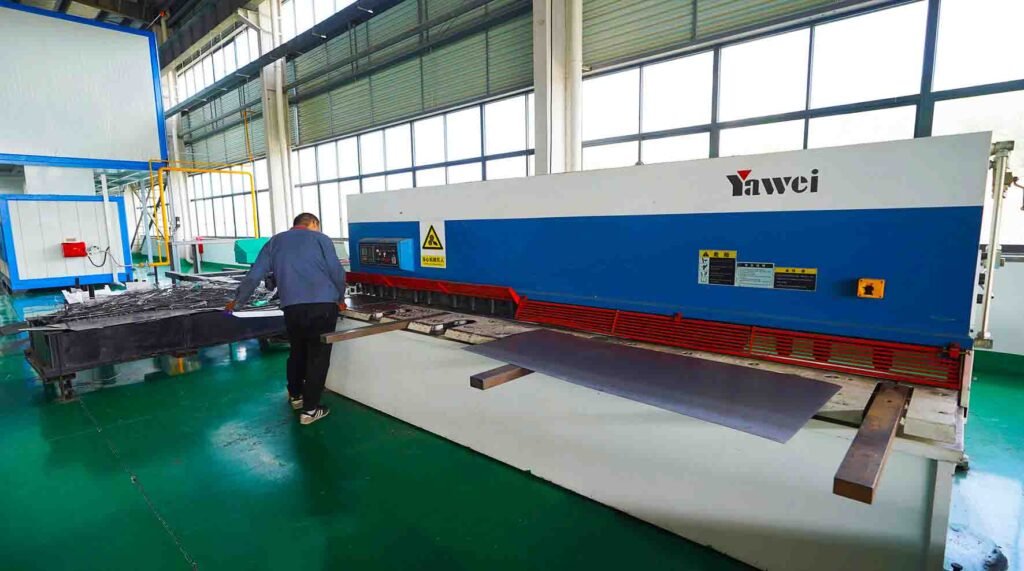
Shearing machine
Through advanced CNC system and sensing technology, it can automatically identify the shape and size of the plate. Precise shearing is carried out according to preset parameters.
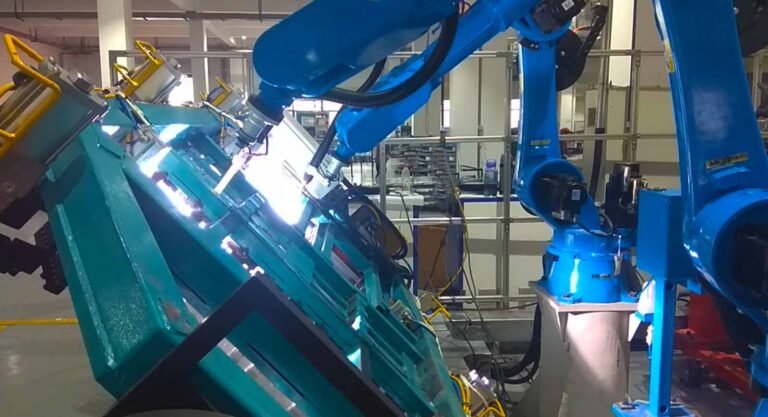
Automated welding robot
Base frame production, fully automated industrial welding robot production line mainly welds genset base frames, trailer chassis, canopy boxes, control cabinets, etc., greatly improving product quality
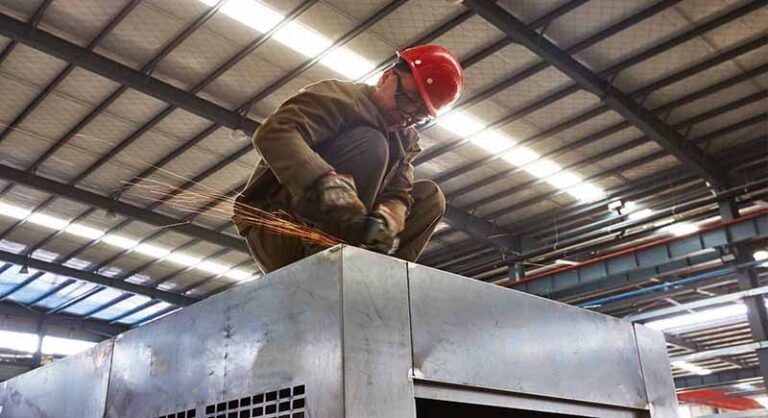
Silent enclosure production
First, high-quality steel is selected, laser-cut, and bent into shape, followed by welding and assembly. Then, soundproof materials such as insulation cotton are installed inside, and finally, the entire unit is debugged to ensure stable performance.

Automatic spraying production line
Silent enclosure spraying: Using corona discharge phenomenon to make the powder coating adsorption on the surface of the workpiece, after heating to make the powder melting, levelling and curing.

Assembly diesel generator set
The assembly process of a diesel generator set includes: chassis installation, engine and generator assembly, connection of electrical and fuel systems, addition of cooling and exhaust systems, installation of the control panel, and finally, debugging and testing.
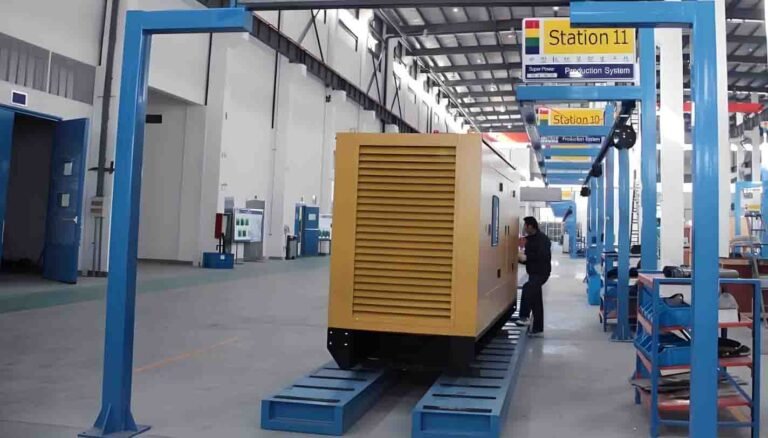
Assembly line equipment station
The main function of the assembly line station for diesel generator sets is to systematize and efficiently assemble diesel generator sets. Its functions include: component inspection and preprocessing, chassis and engine installation, electrical system wiring, cooling system installation, fuel system assembly, and exhaust system installation.
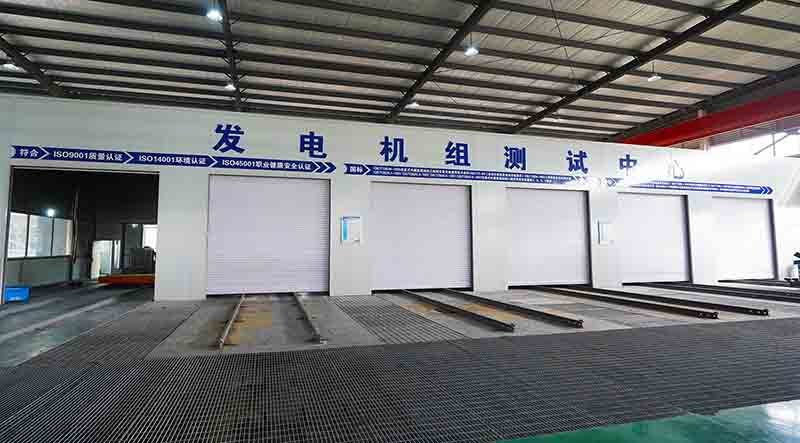
Testing center
Gensets before leaving the factory will carry out 12 tests: appearance inspection, check the complete set, check the signs, insulation resistance test, withstand voltage test, check the starting performance at room temperature, check the phase sequence, check the control panel of each indicator device, measurement of the voltage setting range, measurement of the steady-state voltage deviation, measurement of the steady-state frequency band and measurement of the frequency drop.
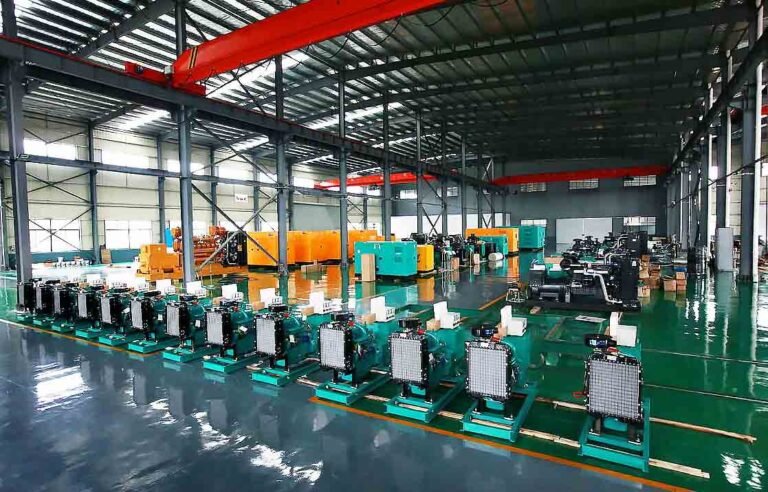
Waiting to be packaged area
In the waiting packaging area, the diesel generator sets have been fully assembled and are neatly arranged, awaiting packaging.

Packaging and delivery
After undergoing rigorous testing and inspection, the diesel generator set undergoes final packaging. This process includes cleaning and inspection, protective packaging, securing with fixtures, and labeling. Once these steps are completed, the generator set is ready for shipment at any time.